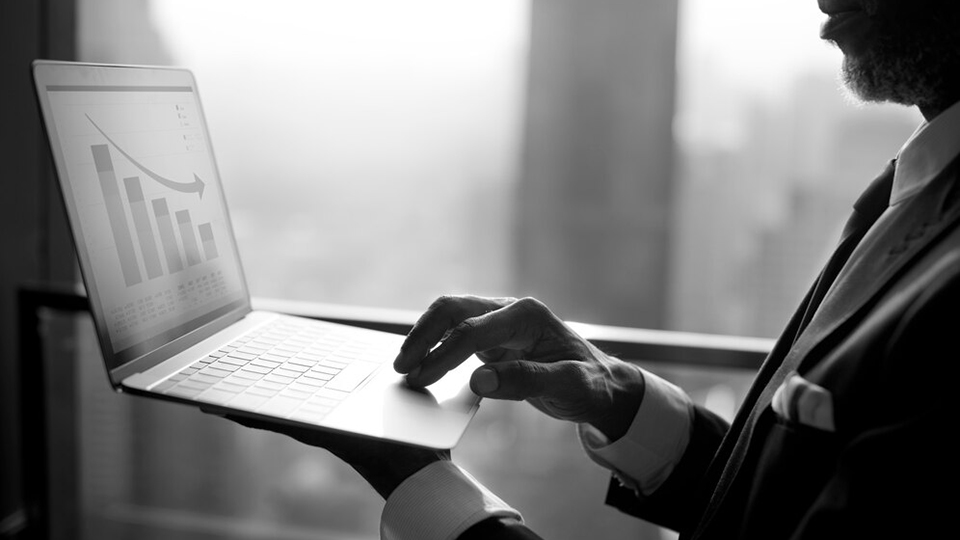
Our Coaching Philosophy
Bringing out the best in teams through targeted, expert-driven performance enhancement strategies. Our mission is getting everybody involved in perfecting things.
Key Coaching Areas
Coaching Methodologies
Coaching Outcomes
Expert Coaches
Connect With Us!
Whether you’re seeking strategic guidance, operational improvement, or industry-specific expertise, our team of experienced professionals is here to support your unique needs. Connect with us today to explore how we can partner with you to achieve lasting success.
Domains
Methodologies
Outcomes
Coaches
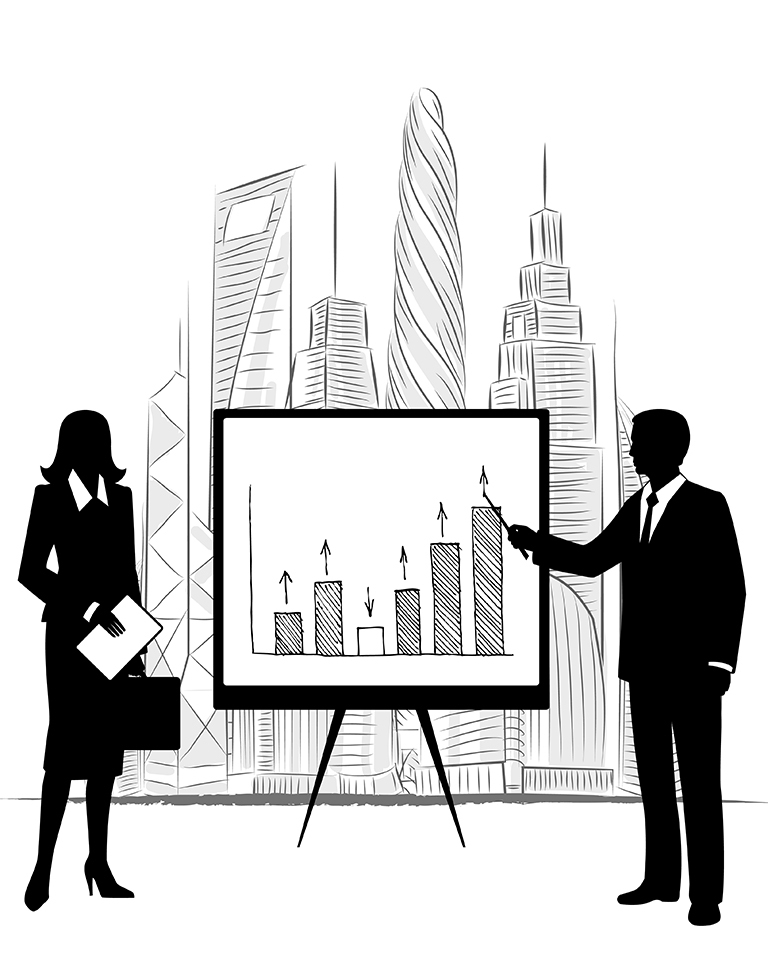
Expert Coaches
Our coaches bring decades of industry experience, specializing in:
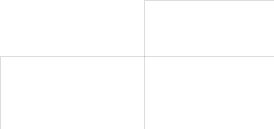