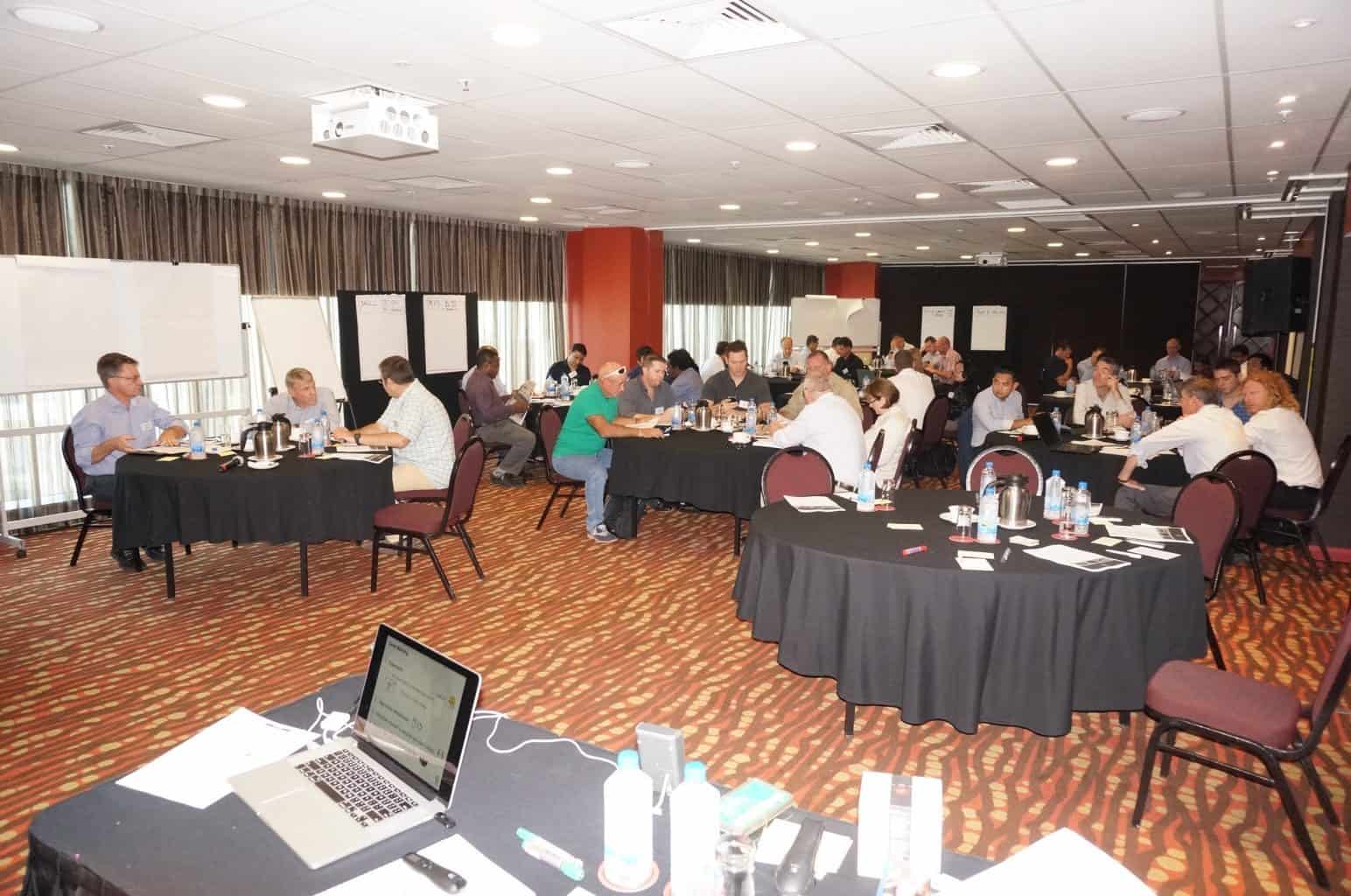
If You Want To Start A Business From Scratch, Focus On The Difference
Well on paper facilitation is a critical service offered by rp-squared (rp²) that focuses on
comprehensive planning and optimization across multiple operational phases.
Key Facilitation Types
Unique Methodology
Tools Utilized
Performance Impact
Facilitation Approach
Connect With Us!
Whether you’re seeking strategic guidance, operational improvement, or industry-specific expertise, our team of experienced professionals is here to support your unique needs. Connect with us today to explore how we can partner with you to achieve lasting success.
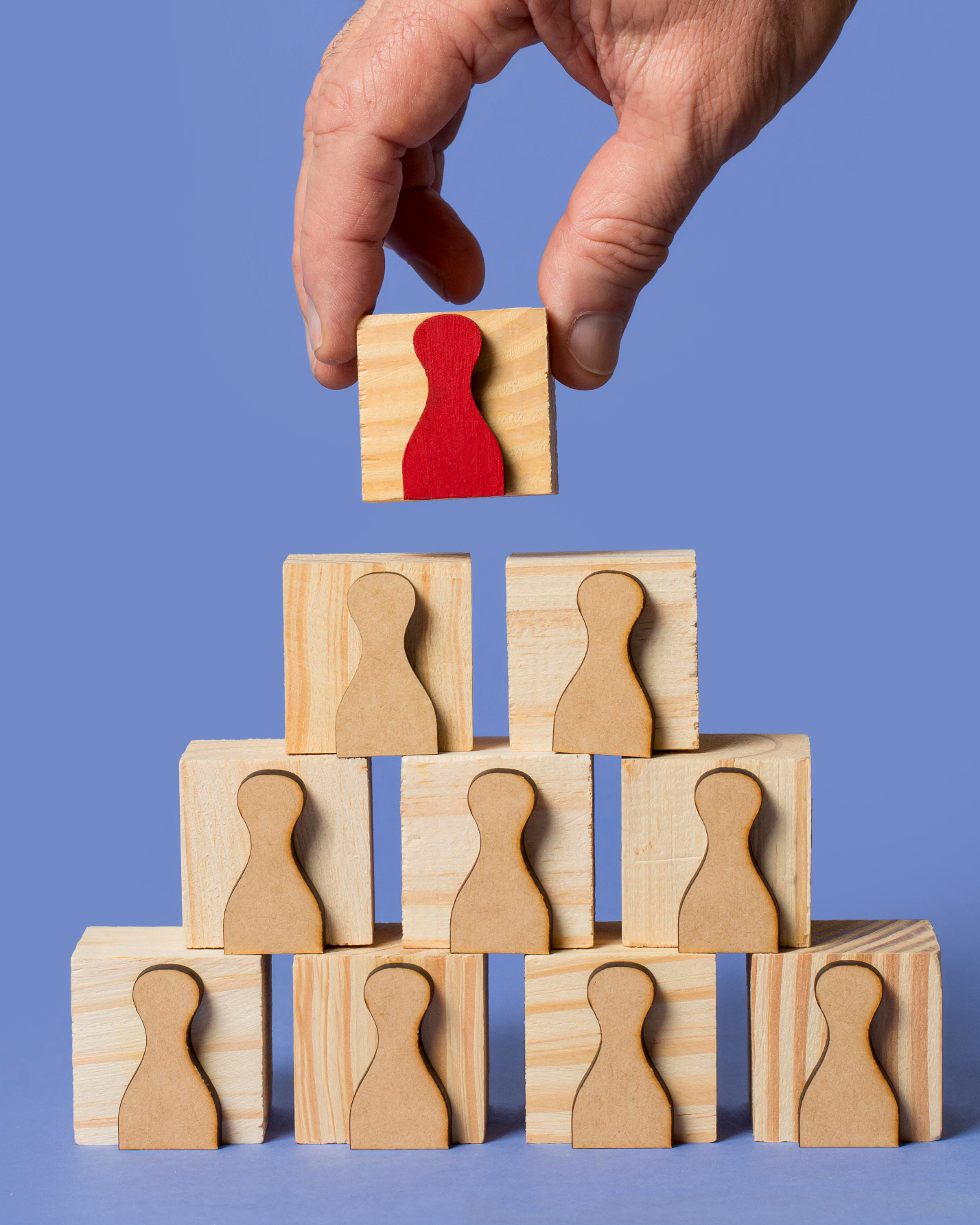
Key Facilitation Types
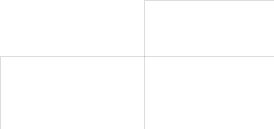
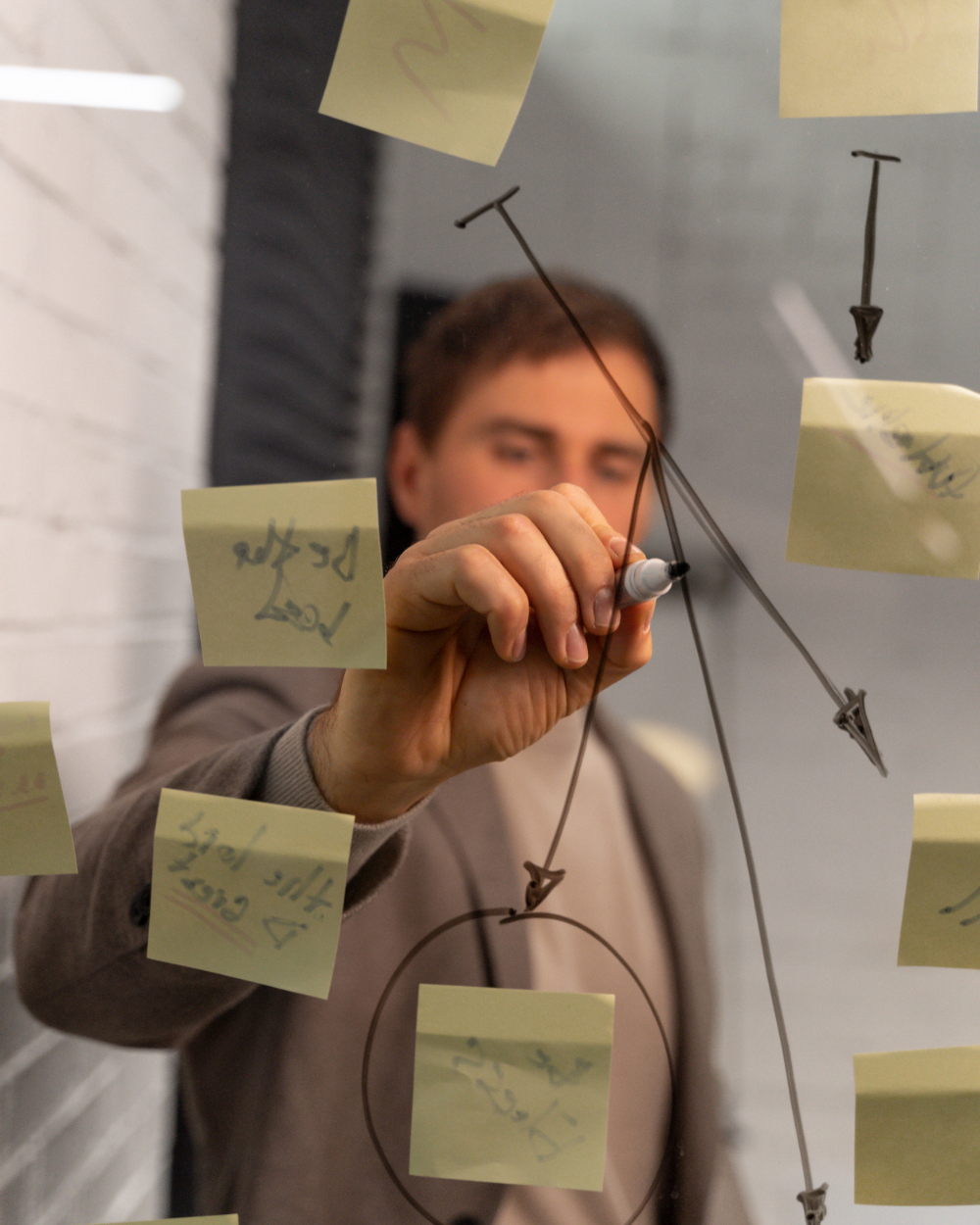
Unique Methodology
The service applies the Technical Limit Methodology, which aims to achieve:
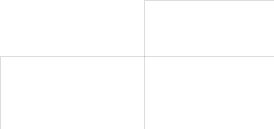
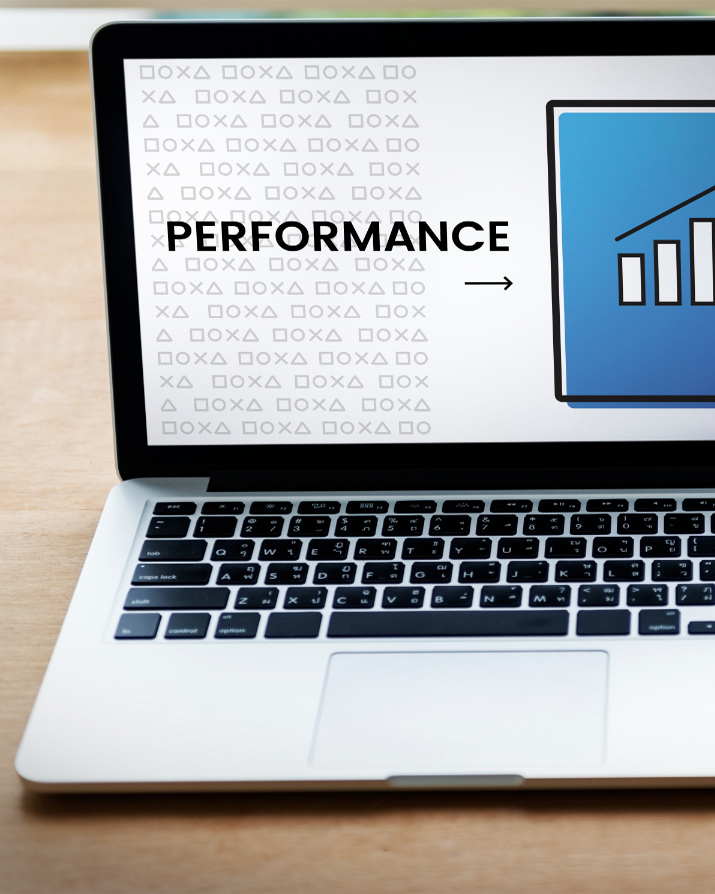
Performance Impact
Clients have experienced remarkable improvements:
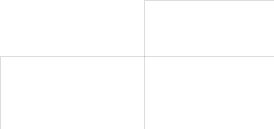
Types
Methodology
Impact
Approach
Utilized
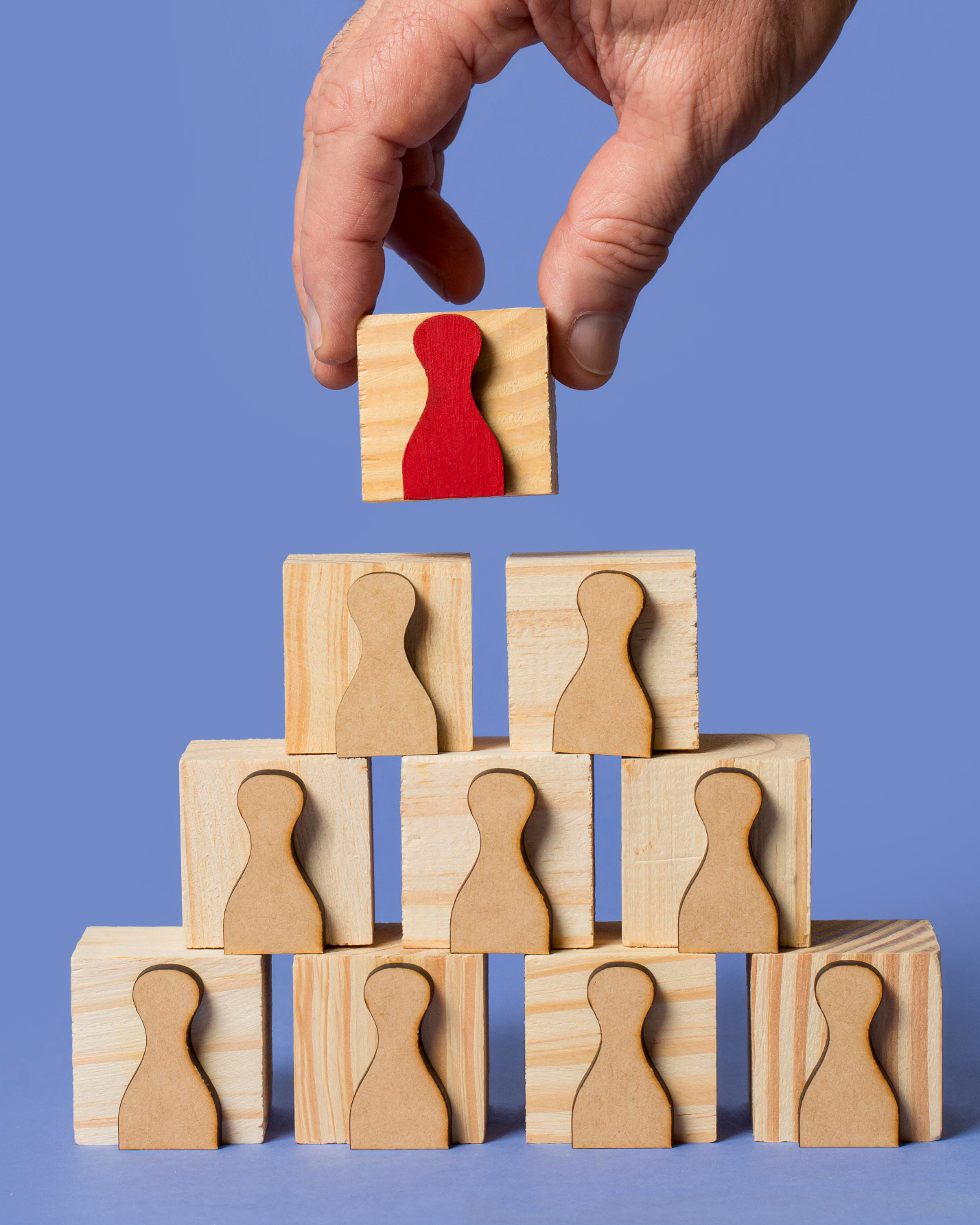
Key Facilitation Types
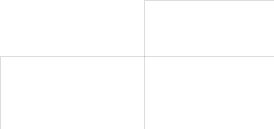
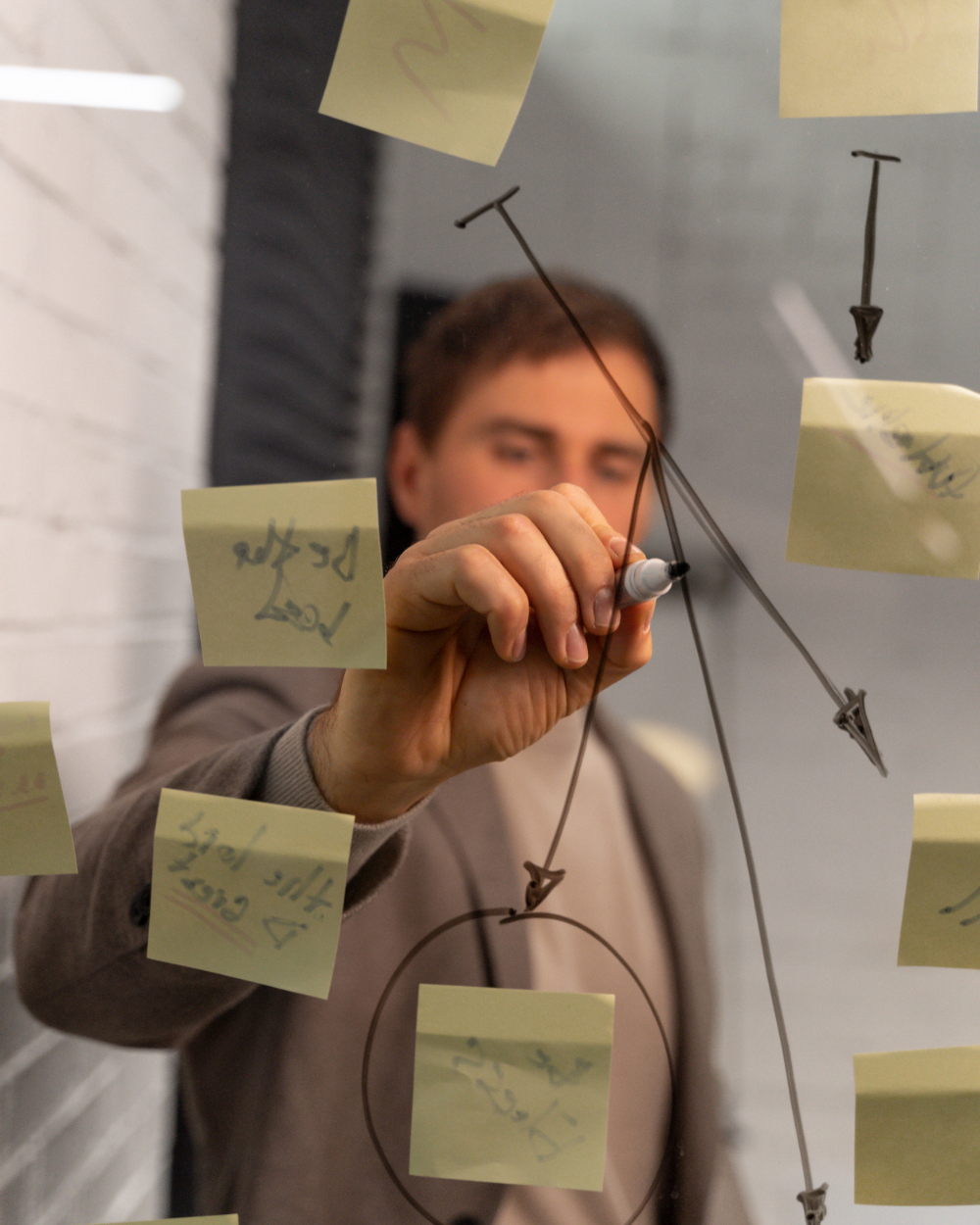
Unique Methodology
The service applies the Technical Limit Methodology, which aims to achieve:
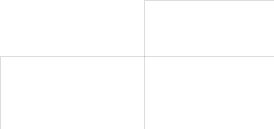
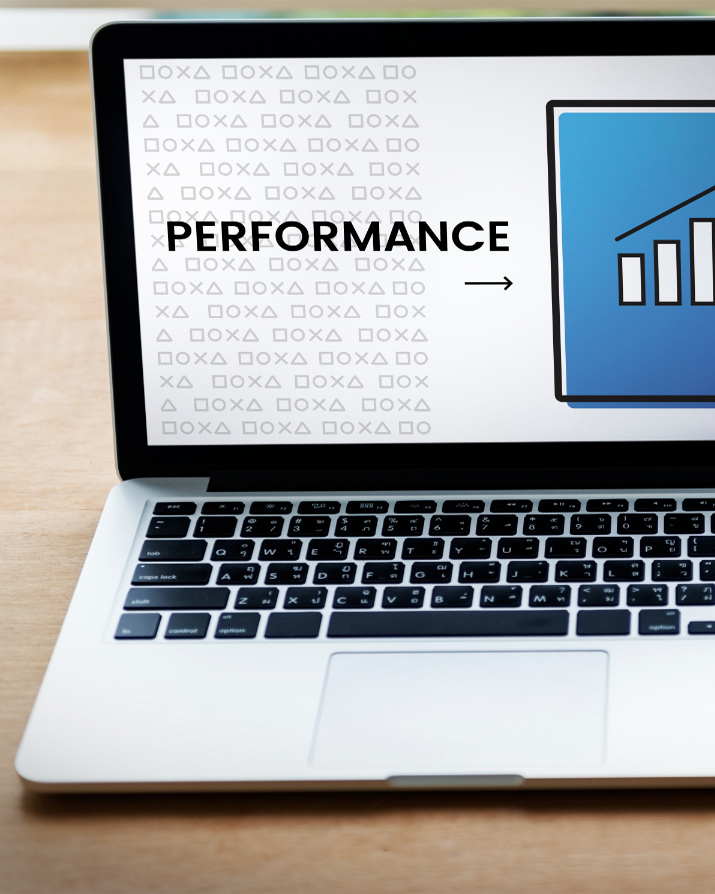
Performance Impact
Clients have experienced remarkable improvements:
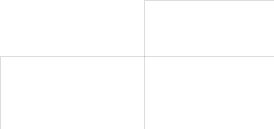