Well Operation Case Study
This job was done for a State Oil Company in South America’s Northeast region. This company produces about 25,000 bopd.
- Home
- Case Studies
- Well Operation Case Study
Case Details
Clients: State Oil Company
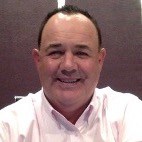
Gordon Duncan
Well integrity, Completions, Interventions & abandonment Expert
Location: South America’s Northeast region.
Let’s Work Together for Development
Call us directly or email us!
Address Business
Email our experts:
The Story
The merger of two major grocery companies held the promise of significant scale advantages, but its success hinged on the meticulous execution of integration. By diligently guiding Company through this complex process, we facilitated a transformative shift in its operating model, organization design, and the effective utilization of synergies across its expanded footprint.
The goal of this project was to perform a PFEA injector and water well design evaluation. The objective was to create a low-cost injector design that met industry standards and well-integrity requirements. This job was done for a State Oil Company in South America’s Northeast region. This company produces about 25,000 bopd.
Background
A Polymer Flood (PF) pilot project had positive results, and a proposal for commercial-scale deployment was authorised in 2013. However, due to the subsequent decline in oil prices and the necessity of financial restraints, the expansion was halted.
Surface and subsurface investigations have begun in order to improve the IRR of the PF expansion. One of the investigations addressed the redesign of injector wells and the selection of wellheads required for polymer expansion.
Three (3) injectors were operational at the time, with annular packers inserted to protect the casing from the injected polymer. However, all three injectors were found to have excessive casing pressures. A new design for injector wells and wellheads was designed based on the lessons learned and the need to reduce the CAPEX of the polymer flood project.
To ensure that the new design complies with all requirements, the designs had to undergo evaluation by an outside expert in the field.
The Completions SME proposed a project to deliver a cost-effective injector well design that meets industry standards and well integrity requirements.
Objectives
The primary goal was to assess whether the design adhered to industry standards and, if necessary, identify which alterations were required to satisfy customer requirements.
Scope
Examine, comment on, and alter suggested injector and wellhead designs for acceptability, usefulness, and cost-effectiveness. Provide formal reasons for design changes that adhere to industry standards.
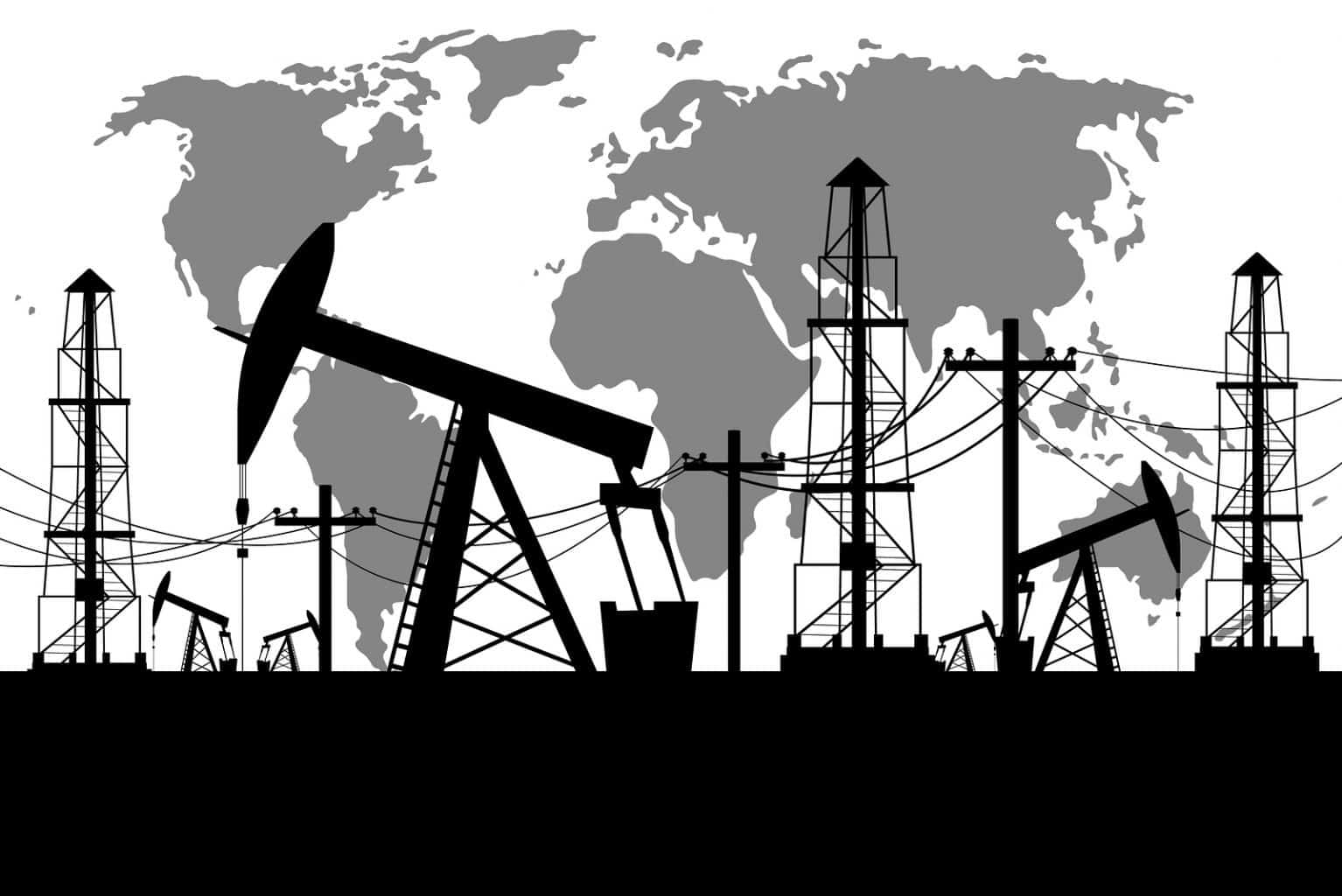
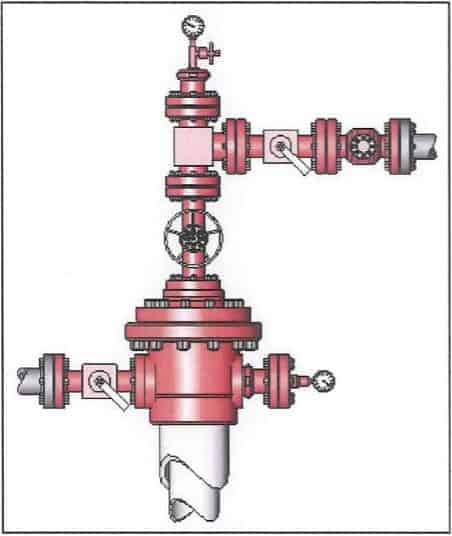
Deliverables
A digitised final report that included the following:
An executive summary; a technical summary; a description of the analysis technique; a brief description of the workflow employed; and any applicable assumptions Conclusions and recommendations are based on the findings and results.
A new well design was agreed upon, and recommendations for possible equipment providers were also given as an added scope to aid local engineers in reaching out to available new technologies.
Data Analysis Chart
The Results
All previous but pertinent documents, including a Major Service Company Injection Well Design assessment and an Injection Well design for CO2 & Polymers, were thoroughly evaluated. There were also memos from the previous ten years on suspected casing leakage and other discoveries.
To cement certainty, add a swellable elastomer-type packer to the shoe joint of the 7′′ Carbon Steel Casing. The casing shoe should likewise be located 100 feet below the water line.
Consider using rod string centralisers to prevent the SRO from excessive movement.
Ensure that the SRO cable is suitable for all injection or generated fluids.
Double-check that the SRO Cable Clips are compatible with all injection fluids.
Think about installing a 3 1/8′′ 2M gate valve with RX 31 compatible SS gaskets.
Ensure that all components of the wellhead system are fluid-compatible.
Consider longer pressure tests for cement verification, and make certain that all charts are witnessed and accepted by the Company Representative.
Consider all Completions Operations Supervised by a Competent Completions Supervisor who understands the need of testing and verification.
Ensure that contingency measures are in place in the event that any operation does not accomplish its objectives.
Finally, analyse the well's lifecycle and how this well could benefit from remediation or a workover.
Summary
A comprehensive technical summary was provided. All components were evaluated for suitability in accordance with current industry standards, and in the absence of such standards, good oilfield practise was used.
Applicability of the Wellhead
Well Integrity
Well barrier plan
Verification of the final well barrier
Contingency planning for well construction
Well design deliverables, reporting and documentation
Barrier verification
Casing & Tubular connections
Well handover information
Well operational phase objectives
Well monitoring and surveillance
Monitoring and surveillance frequency
End of well life review
Protection of Freshwater Zones
Resistance to Corrosion and to Avoid Polymer Contact with Carbon Steel
Cost Effectiveness Durability
Review Process
Conclusions and Recommendations
Giles and his team at Herrington Business Consulting have been absolutely great to work with and they definitely have gone above and beyond for us by streamlining all of our accounts so that we can focus on what we do love to do and continue to grow our business. Morbi venenatis ut sapien eu lobortis.
